Transforming Industries: The Importance of Plastic Injection Moldings
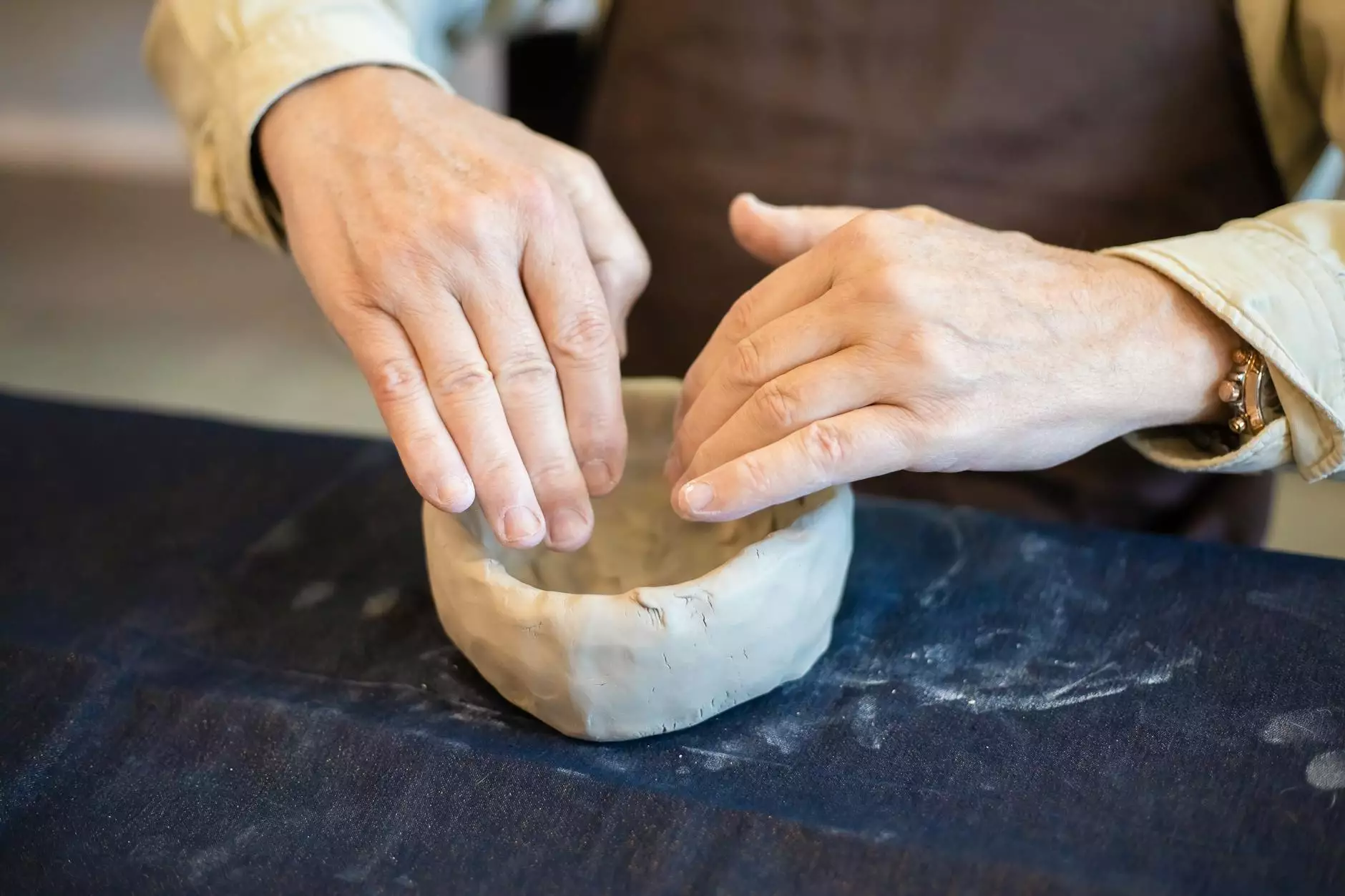
In the fast-paced world of manufacturing, plastic injection moldings have emerged as a cornerstone technique, particularly in industries such as electronics and medical supplies. With advancements in technology and materials, the capabilities of plastic injection molding continue to grow, enabling manufacturers to produce high-quality, complex components efficiently. This article delves into the significance, processes, benefits, and applications of plastic injection moldings, showcasing how companies like Nolato have leveraged this technology to enhance their operations and product offerings.
Understanding Plastic Injection Molding
Plastic injection molding is a manufacturing process used to produce parts by injecting molten plastic into a mold. The process begins with the creation of a mold, which is designed based on the specifications of the desired part. Once the mold is ready, plastic pellets are heated until they become molten and are then injected into the mold under high pressure. After the plastic cools and solidifies, the part is ejected, and the cycle can be repeated.
The Process of Plastic Injection Molding
- Designing the Mold: The first step involves designing the mold, which must precisely shape the desired part. Advanced computer-aided design (CAD) tools are often used to create detailed models.
- Material Selection: Choosing the right type of plastic is critical. Various thermoplastics and thermosetting plastics can be used, depending on the desired properties of the final product.
- Heating and Injection: The selected plastic material is heated to its melting point and then injected into the mold, filling it completely.
- Cooling and Ejection: Once filled, the mold is cooled to solidify the plastic. After this process, the finished part is ejected from the mold.
Advantages of Using Plastic Injection Moldings
The use of plastic injection moldings offers numerous advantages, making it a popular choice among manufacturers. Here are some of the key benefits:
- High Efficiency: The injection molding process can produce thousands of identical parts quickly, making it ideal for large-scale production runs.
- Complex Geometries: It allows for the creation of intricate shapes that would be difficult or impossible to achieve with other manufacturing methods.
- Material Versatility: A wide range of plastics can be used, each with different properties including durability, flexibility, and resistance to chemicals.
- Reduced Waste: The process is highly efficient in raw material usage, as excess plastic can be recycled and reused.
- Cost-Effectiveness: While there are initial costs associated with mold creation, the high-volume production can lead to lower per-unit costs in the long run.
Applications in the Electronics Industry
The electronics industry is one of the largest sectors benefiting from plastic injection moldings. Components such as housings, switches, and circuit boards are manufactured using this technology. The precise nature of injection molding makes it possible to produce parts that meet the stringent specifications of electronics manufacturing.
Key Applications in Electronics
- Smartphones: Cases, buttons, and internal components are often made from injection-molded plastics, offering a lightweight and durable solution.
- Consumer Electronics: Devices such as televisions and audio systems utilize injection-molded parts for both structural and aesthetic components.
- Computers: From casings to intricate internal connectors, injection molding is essential in producing reliable computer hardware.
Importance in the Medical Supplies Sector
In the medical supplies industry, plastic injection moldings play a crucial role in producing components that must meet strict safety and efficacy standards. The precision of injection molding enables the creation of complex devices that are essential for medical applications.
Key Applications in Medical Supplies
- Medical Devices: Components for surgical instruments, diagnostic devices, and other equipment are often produced using injection molding to ensure precision and reliability.
- Disposables: Items such as syringes, IV bags, and medication containers are typically made with injection-molded plastics to maintain sterility and save costs on production.
- Prosthetics and Implants: Custom-molded parts are essential in creating implants and prosthetics tailored to individual patient needs.
Challenges and Solutions in Plastic Injection Moldings
While plastic injection moldings offer exceptional advantages, there are challenges that manufacturers may face:
Common Challenges
- High Initial Costs: The creation of molds can be expensive; however, these costs can be amortized over large production runs.
- Material Limitations: Not all materials have the same properties, and selecting the right one is crucial for product performance.
- Quality Control: Maintaining consistent quality across large volumes can be challenging and requires effective monitoring processes.
Effective Solutions
To overcome these challenges, companies have implemented various strategies:
- Investment in Technology: Utilizing advanced molding machines and automation helps enhance efficiency and reduce costs.
- Material Innovation: Ongoing research into new materials leads to better-performing plastics that can meet diverse application needs.
- Quality Assurance Programs: Implementing stringent quality control measures ensures that each produced part meets high standards.
How Nolato Leads the Way in Plastic Injection Moldings
Nolato is a prime example of a company successfully leveraging plastic injection moldings in both the electronics and medical supplies sectors. With a commitment to innovation and excellence, Nolato has established itself as a leader in the manufacturing of high-quality plastic components. Here’s how:
Commitment to Quality
Nolato adheres to stringent quality standards, ensuring that every part produced through plastic injection moldings meets or exceeds industry expectations. Their state-of-the-art manufacturing facilities are equipped with the latest technology, allowing for precise control over the injection molding process.
Focus on Sustainability
As sustainability becomes increasingly important, Nolato has embraced eco-friendly practices. This includes using recyclable materials and reducing waste during the injection molding process, aligning their operations with global sustainability goals.
Innovation at the Core
Nolato continually invests in research and development, exploring new materials and technologies that enhance the capabilities of plastic injection moldings. This forward-thinking approach ensures they stay ahead of industry trends and can meet the evolving needs of their clients.
Conclusion: The Future of Plastic Injection Moldings
The future of plastic injection moldings looks promising as industries continue to advance in technology and product design. With the growth of the electronics and medical supplies sectors, the demand for efficient, high-quality manufacturing processes will only increase. Companies like Nolato are well-positioned to meet this demand, driven by their commitment to innovation, quality, and sustainability.
In summary, as businesses seek to enhance their production capabilities while adhering to quality and safety standards, they will find that plastic injection moldings provide the ideal solution. By harnessing this powerful manufacturing technique, industries can create the next generation of products that meet consumer needs and improve lives.