The Essential Role of China Die Casting Factories in Modern Manufacturing
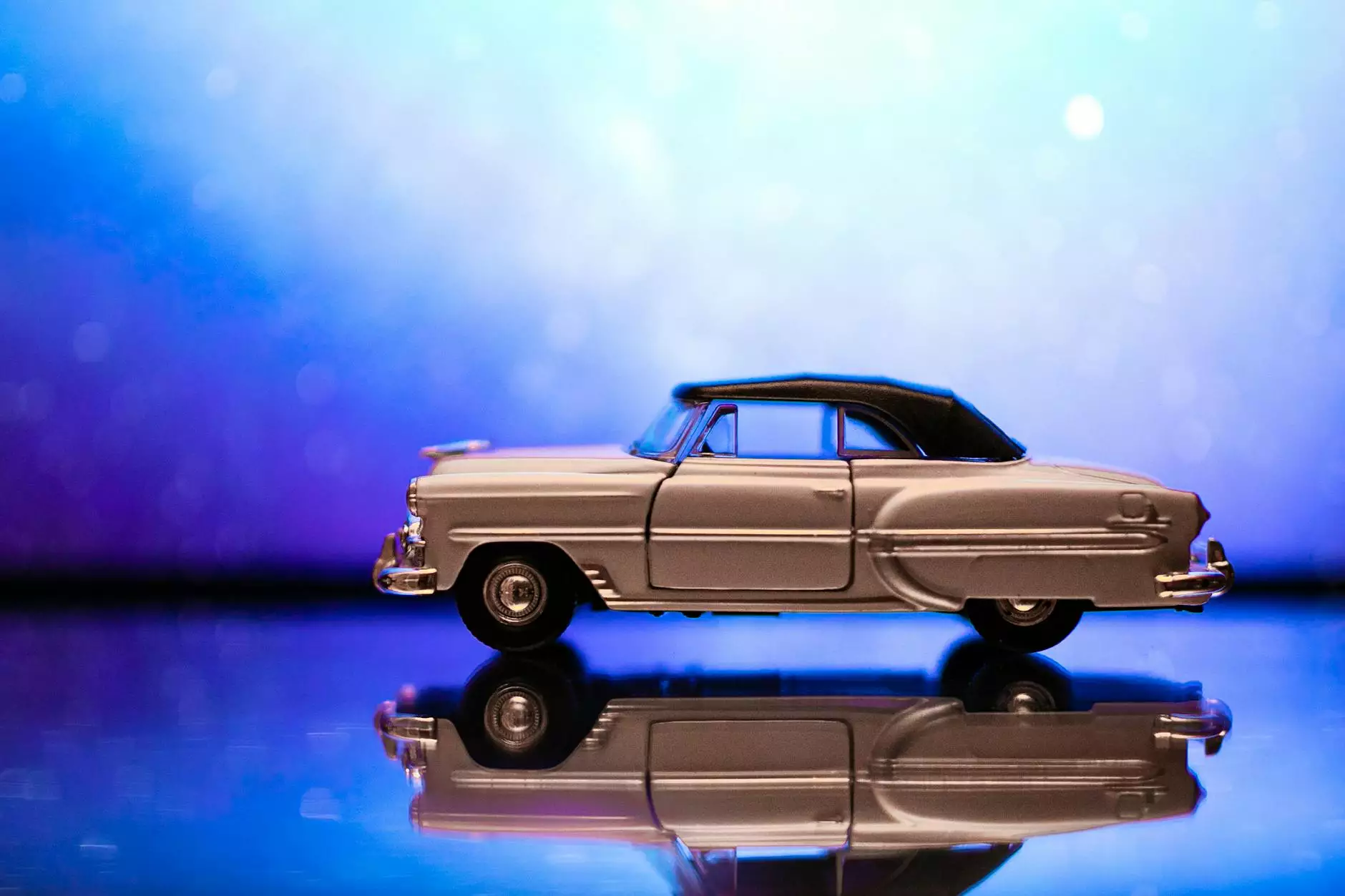
In today's competitive global market, the manufacturing industry has experienced significant evolution, especially in the field of die casting. Among various techniques, die casting stands out for its precision, efficiency, and the ability to produce intricate designs. China, renowned for its manufacturing prowess, hosts numerous China die casting factories that serve various industries worldwide.
What is Die Casting?
Die casting is a metal casting process characterized by forcing molten metal under high pressure into a mold cavity. The process allows for high-volume production of parts with excellent dimensional accuracy, smooth surfaces, and minimal machining required post-production.
Types of Die Casting
There are several types of die casting processes, each suited for different applications:
- High-Pressure Die Casting: This method involves injecting molten metal into a steel mold at high pressure, ideal for high-volume production.
- Low-Pressure Die Casting: Here, molten metal is poured into a mold under low pressure, used primarily for larger parts where high precision is needed.
- Gravity Die Casting: Utilizes gravity and manual processes to fill the mold, typically used for lower volume production.
- Squeeze Die Casting: Combines high-pressure injection with slow filling, improving metal flow and reducing defects.
Why Choose China for Die Casting?
China has established itself as a leader in the die casting industry due to several compelling reasons:
- Cost-Effectiveness: With lower labor and production costs, China die casting factories provide competitive pricing for high-quality cast parts.
- Advanced Technology: Many Chinese factories utilize state-of-the-art machinery and technologies, leading to improved efficiency and reduced defects.
- Skilled Workforce: The availability of a skilled workforce, well-versed in modern manufacturing techniques, ensures quality output.
- Global Supply Chain Integration: China’s established supply chain networks facilitate faster delivery and reduced lead times for manufacturers worldwide.
The Manufacturing Process in China Die Casting Factories
The process followed in China die casting factories is meticulously structured to ensure quality and efficiency. Here is an overview of the typical die casting process:
1. Design and Tooling
Every successful die casting project begins with a thorough design phase. Engineers use CAD software to create detailed designs, which are then transferred to tooling. High-quality steel molds are manufactured to meet the exact specifications.
2. Melting and Pouring
Once the tooling is in place, the process involves melting the metal—commonly aluminum, magnesium, or zinc. The molten metal is carefully poured or injected into the mold using high-pressure machinery.
3. Cooling and Ejection
After the mold is filled, the molten metal cools and solidifies. Once cooled, the mold is opened, and the finished parts are ejected. This stage may include additional processes, such as trimming or cleaning.
4. Surface Finishing and Quality Control
The finished cast pieces may undergo several surface finishing processes to meet customer specifications. Rigorous quality control checks ensure that every piece complies with industry standards and client expectations.
Applications of Die Casting in Various Industries
The versatility of die casting enables its application across numerous sectors, including:
Automotive Industry
Automotive parts, such as engine components, transmission housings, and structural frames, benefit significantly from the strengths of die casting. The lightweight and durable properties of die-cast items contribute to energy efficiency and performance.
Aerospace Sector
In aerospace, the need for precision and reliability is critical. Die casting offers the ability to create components that meet stringent safety and performance standards, such as brackets, housings, and control components.
Consumer Electronics
Manufacturers of consumer electronics utilize die casting for producing housings, frames, and components that require fine tolerances and a sleek finish, critical for aesthetics and functionality.
Environmental Considerations in Die Casting
With increasing awareness of environmental impacts, China die casting factories are adopting eco-friendly practices. This includes:
- Recycling Materials: Many factories focus on utilizing recycled metals, greatly reducing the environmental footprint.
- Energy Efficiency: The implementation of energy-efficient technologies in die casting processes minimizes energy consumption.
- Waste Reduction: Advanced processes and practices are in place to reduce waste generated during die casting, promoting a circular economy.
Choosing the Right China Die Casting Factory
Finding the right partner among China die casting factories is essential for success. Consider the following criteria when making your choice:
- Capabilities: Ensure the factory has the necessary technology and experience to handle your specific requirements.
- Quality Assurance: Look for factories that have robust quality control processes and certifications to guarantee product excellence.
- Communication: Efficient and clear communication channels are essential for a smooth partnership and timely project updates.
- Customer Reviews: Researching past customer experiences can provide insights into the reliability and performance of potential factory partners.
The Future of Die Casting in China
The scope for die casting manufacturing in China continues to thrive. Innovations in materials and processes, alongside advancements in sustainability practices, are setting a promising trajectory for the future. The integration of Artificial Intelligence (AI) and Industry 4.0 strategies is expected to further enhance operational efficiencies.
Emerging Trends
Some emerging trends that are shaping the future of die casting include:
- 3D Printing Prototyping: The integration of 3D printing technology is enhancing prototyping processes, making it faster and more cost-effective for design validations.
- Smart Factories: Automation and IoT are leading towards the development of smart factories, which will enhance data exchange and operational monitoring.
- Material Innovations: Research is ongoing into new alloys and composites that can provide superior performance while remaining lightweight.
Conclusion
China die casting factories play a critical role in the global manufacturing landscape, providing robust, efficient, and accurate solutions across numerous industries. As technology progresses and sustainability becomes increasingly pivotal, these factories are poised to lead the way in innovation and excellence. By understanding the die casting process and leveraging the capabilities of these factories, businesses can drive growth and maintain a competitive edge in their respective markets.